To Fill a Drastic Need
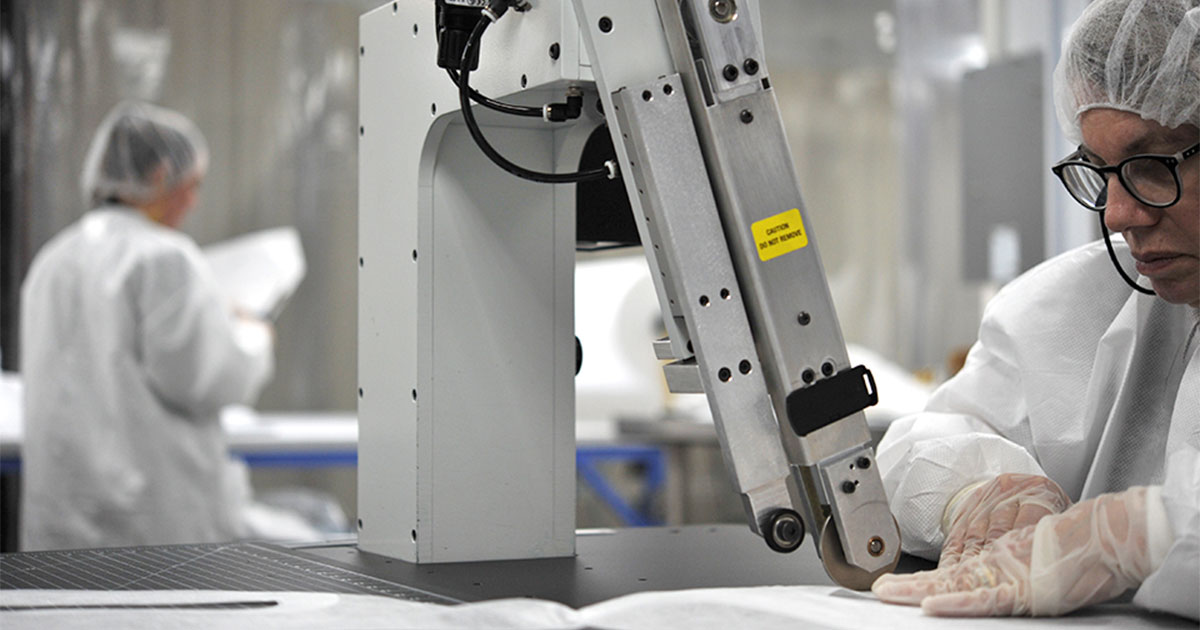
At first glance, the problem seems easy enough to figure out. To fill the urgent need for medical masks, why not just ask manufacturers, particularly those in the medical space, to start cranking them out? After all, their job is to make stuff.
Turns out, producing a new product, one that you have no previous experience with, does take time and effort to do right. There are supply chain needs to meet, and technical issues to fix, and testing to be done.
Based in Boston and Lee, Massachusetts, Boyd Technologies is taking on the challenge. “We’re working on this 24/7 right now,” says Matthew Boyd MBA’07, the company’s chief commercial officer. “This is a tremendous crisis. There is a lot of confusion around what can and cannot be done. We want to provide solutions.”
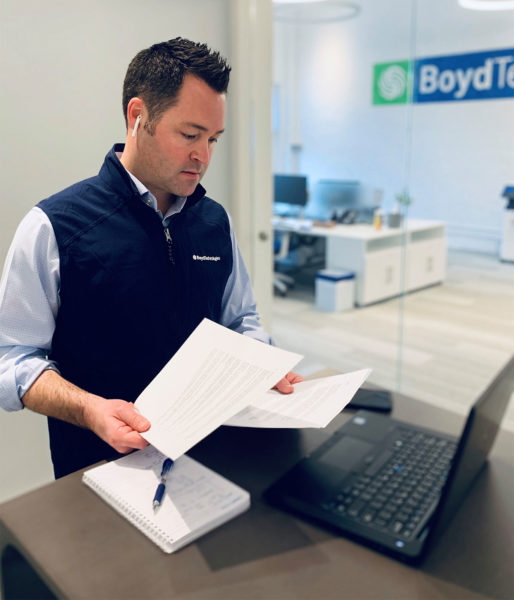
A provider of material sourcing, product development, and manufacturing services, Boyd Technologies is a family affair. Matthew’s father, Bronly, founded the company in the late 1970s. Matthew’s older brother, Stephen, is CEO. The company has deep roots in New
England, and as the coronavirus pandemic unfolded and the dire need for medical masks became dangerously apparent, the Boyds thought of their local hospital workers and first responders.
“This is very personal to us,” says Matthew Boyd. “We feel a part of the community. We are a family business that resides here. We feel privileged to be here. We feel an obligation to help.”
A Lot of Work
Boyd Technologies focuses on developing and making single-use medical devices, as well as over-the-counter drugs, but it doesn’t normally produce and distribute medical masks. “This is not an existing core business,” says Matthew Boyd.
To fill the need for masks, the company is taking a multipronged approach. In the near term, it is reaching out to its global contacts to track down masks that other manufacturers already have made. “We were able to step in quickly,” says Boyd. “We have a global supply chain. We work with manufacturers all over the world.”
The company also is working to make its own masks. A number of its production lines are well suited for the task, but finding the proper materials to make the masks is an obstacle. “The raw materials are where the backlogs are,” says Boyd. “We know the supply chain as well as anyone. We have looked at materials that are suitable replacements and that do not have a backlog.”
“This is a tremendous crisis. There is a lot of confusion around what can and cannot be done. We want to provide solutions.”
Matthew Boyd MBA'07
Beyond finding materials, the company is modifying its manufacturing equipment to produce a mask prototype. That prototype will then need to go through a round of testing, and if that goes well, the mask will go to the Food and Drug Administration for emergency use authorization.
“It’s quite a lot of work,” says Boyd.
In the Long Term
Boyd Technologies may be helping to fill a critical, short-term need, but in the long term, it still wants to continue making medical masks. The company hopes to play a role in providing a stable domestic supply of masks in the future, so that shortages aren’t an issue going forward.
To do that, the company would like to return to the contract manufacturing, in which Boyd produces products that a brand then sells and distributes, that is its normal way of doing business. That means the company will be looking for a brand to team up with.
“We view ourselves as a reliable partner in the long term,” says Boyd. “We aim to be on the front end of the most high-performing products in this space.”
Posted in Community