Peter Shepard, MBA’96: Novomer was a way to take my experience and apply it to do something good.
Peter Shepard, MBA’96, works in a world that most of us don’t think about or, frankly, understand. As chief business officer for Novomer, an emerging chemistry company, he deals with waste gases and catalysts and polymers. To the rest of us, these substances help make things sticky or durable or cushy. Some day, the glue your daughter uses in art class, or the paint you buy to finish a table, or that comfy mattress you purchase could contain Novomer’s products.
What makes Waltham, Mass.-based Novomer different from its competitors is its technology. Most of Novomer’s competitors rely heavily on costly, nonrenewable fossil fuels to make chemicals and materials. But an important part of Novomer’s business model is sustainability, a word not often associated with this industry. Using catalysts, Novomer transforms carbon monoxide, a toxic waste, and carbon dioxide, a greenhouse gas, into polymers that can be used in the above-mentioned products and more. As such, it hopes to benefit the environment by creatively using pollutants, while reducing the need for petroleum.
At the same time, says Shepard, its products still will offer high performance and cost advantages over those of its competitors. “That’s what really gets people excited,” he says. “If people only saw it as a green polymer, we’d have closed up shop long ago.”
All of this sounds fantastic. Now Novomer just has to do it. Bringing a new polymer to market, however, is no easy task. “I don’t know if I can name a brand new polymer that has successfully come to market in the last 10 years,” says Shepard. “People don’t do it because it’s so hard.”
Shepard knows from experience the obstacles Novomer faces. As an undergraduate at Rensselaer Polytechnic Institute, he studied chemical engineering. His first job out of school was as a process engineer with an industrial chemical company, producing “all these horrible, nasty chemicals.” He then worked for Cabot Corp., a giant in the chemical and performance materials industry, for about 16 years. While there, he switched over to the commercial side of the business. In what Shepard calls a “great intrapreneurial opportunity,” he helped launch a new business for the company, developing a pigment technology originally used for tires into a product for what at the time was a nascent printer market. “We created a profitable business serving the inkjet printer market that today is very valuable to Cabot,” says Shepard.
After leaving Cabot and running a nylon manufacturer for a few years, Shepard consulted for and then joined Novomer. “That was around 2007, and at the time green technologies were coming into the spotlight,” he says. “I thought Novomer was an interesting way to take my experience and apply it to do something good, but also create a sustainable business.” In this case, by sustainable he means a business that has a return on investment.
Novomer had just raised its first round of venture funding when Shepard joined. The company had an interesting technology and bright scientists, he says, but not a lot of business or industry experience. “They needed somebody who understands how these markets work, what things you have to demonstrate to really get commercial traction,” he says. “So it seemed like a great fit for me.”
During the next six years, the company would start “peeling back the onion,” as Shepard puts it, figuring out the capabilities—and limitations—of the technology. Novomer is pursuing two technical platforms. One focuses on carbon monoxide, using it to produce acrylic acid, a precursor to super-absorbent polymers. “It’s biggest use is in diapers,” says Shep-ard. “This technology is a little further behind in terms of development, but the advantage we’ll bring is cost. The use of carbon monoxide is relatively inexpensive compared to petroleum feedstocks. We’re in the midst of selecting a partner that brings process capabilities so we can demonstrate the technology at an industry-relevant scale.”
On the carbon dioxide side of its business, Novomer is closer to market. At one time, the company thought it would be able to create thermal plastics used in products such as cups and bottles. But as researchers delved deeper into the technology, they realized the plastic lost its shape if it grew warm from just sitting in the sun. “Obviously, that was a real limitation,” says Shepard. “We looked at a bunch of ways to get around that. There are ways of doing it, but at the end of the day, there were too many issues that our customers would have to go through to use the product, so we put that on the shelf.”
Novomer’s efforts to make polyols (a type of polymer) that can be used in foams, adhesives, and coatings, however, have proved more successful. The company is working with about 100 customers, says Shepard, who are giving Novomer valuable feedback. “We’ve made what we call a generic representation of our product, and we sample that to our customers. They might say, ‘We want a higher molecular weight, because it gives better performance.’ Or, ‘We want this functionality, because it will react better with the other ingredients in our formulation,’” says Shepard. “So we’ve done this purposefully to get this kind of feedback. And some people say, ‘I like that product. I want to buy it.’”
Some of those potential customers are in the coatings industry, such as Sherwin-Williams, PPG Industries, and AkzoNobel. Others, such as 3M and Henkel, create adhesives based on Novomer’s product. Manufacturers of automotive interiors—Johnson Controls, Lear—are on Novomer’s radar, as are the big mattress and foam companies, such as Tempur-Pedic. “We’re right on the cusp of going from sampling and R&D to commercial sales,” says Shepard.
When Shepard started with Novomer, he honestly wasn’t sure he would ever utter those words. Asked what he thought about the probability of failure back then, he pegged it at 99 percent. “Nobody had done this before,” he says. “We didn’t know what we know now. So we placed our bets. You learn as you move down the path.” Today, however, he reverses those odds, believing Novomer has a 99 percent chance of succeeding. The opportunities exist, he says. The questions that remain are: How big are those opportunities, and can Novomer claim a stake?
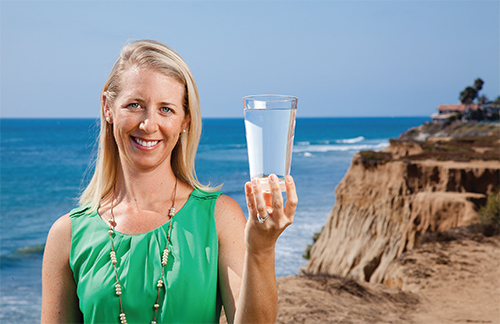
Photo: Chris Giles
Jessica Jones ’00: I feel very passionately about the Carlsbad project. It’s not just a job to me.
Uncharted Waters
After graduating from Babson, Jessica Jones ’00 moved West to San Diego. Having grown up in New Hampshire, she wanted to try living in a warmer climate. Soon after arriving, she landed a job as an administrative assistant at Poseidon Water, a U.S.-based developer and financer of desalination plants.
At the time, the job was simply a way for Jones to settle in to a new environment. She needed a paycheck, and Poseidon, being new to the area as well, needed an employee. “When I started, there were only three of us,” says Jones.
Poseidon had just secured land in Carlsbad to build what it hoped would be the largest seawater desalination plant in the Western Hemisphere at a cost of about $1 billion. Popular in other parts of the world, desalination hasn’t gained much of a following in the United States. (“In the Middle East, there are projects five times the size of this one,” says Jones.) The cost of building and running these plants, along with the availability of alternatives such as conservation and reclamation (retreating and reusing wastewater) and an uncertainty around the plant’s environmental impact, often dissuade officials from choosing the desalination route.
In San Diego County, however, about 80 percent of its drinking water comes from Northern California and the Colorado River, giving the county little control over this valuable resource. Droughts in the not-so-distant past coupled with a growing population and predictions of water crises finally convinced officials to move ahead with developing a desalination plant as part of an overall strategy to diversify its water supply.
As the Carlsbad project moved ahead, Jones’ job morphed into assistant project manager. She worked on all aspects of development, from scheduling to finance to marketing. But the permitting process, which took six years, proved the most trying. Part of the delay came from lengthy government processes, but an environmental group opposed to the costs and in favor of reclamation also issued 14 lawsuits.
To help, Jones took charge of community education and outreach. She became intimate with the arguments against the plant so that when she held community meetings or would speak to various organizations, she was prepared. The water will be twice as expensive. True, but the contract with the county is a fixed price, and projections bring those costs in line in a few years. Its water may even cost less some day. The plant uses too much energy. Desalination uses about 30 percent more energy than importing water, but the plant installed solar panels and is employing energy recovery. It’s also committed to a zero carbon footprint. What about environmental damage? The company conducted and passed numerous environmental tests from the Scripps Institution of Oceanography and other institutions. No damage was detected from the discharge. On the intake, a small amount of larvae is killed. To mitigate, Poseidon is restoring 66 acres of wetlands in San Diego County.
Jones also developed relationships with key leaders. At public hearings, she would rally supporters and ask them to speak in favor of the plant. Since 2003, Poseidon has had a pilot plant, used not only for testing the technology and pretreatment systems, but also for running public tours, which Jones often leads, and giving people a chance to taste the water. Eventually, all the lawsuits were either thrown out or won by Poseidon, which moved past the permitting phase and into construction at the end of last year.
Since attaining its permits, Poseidon hasn’t heard from the environmental group. “I don’t think they’re gone,” says Jones, who acknowledges the group’s concern but has become a believer in employing desalination as part of a water strategy. The plant won’t solve all of the county’s problems. When up and running in late 2015, it will produce 50 million gallons of water a day, which serves about 300,000 people, or 7 percent of the county’s needs. “We don’t just need desalination,” she says. “Reclamation and conservation should be part of the effort. But it’s hard to do these things when you don’t have water to begin with.”
In the meantime, Poseidon has grown to about 30 employees in the U.S. (10 in Carlsbad) and is developing other large-scale desalination plants in California, Florida, and Texas. Jones is focusing on supporting the Carlsbad plant and pipeline construction. “The plant is easy,” she says. “There’s very little impact on anyone from the construction.” The 10-mile pipeline that will deliver the water, however, is another story. It’s almost 5 feet in diameter and about 20 feet underground, passing through both residential and commercial areas.
Jones doesn’t try to cover up the impact. “It’s very intrusive to residents,” she says. “The right of way for the city in some cases goes halfway up their front lawns. We’ve had to tear out yards and driveways. So I’ve been working to get the information out there about what is happening and when it will occur. When people have individual complaints, my big motto is: Call us. Don’t call the mayor. I want to be able to take care of all concerns.” When finished, Poseidon and its contractor restore and replace what was torn apart to its previous or better condition.
The section of pipeline that runs through residential areas is almost complete, says Jones, but the next section runs down a commercial street, raising a whole new set of concerns. “There’s a huge business park that has 900 tenants,” says Jones. “They’ve been very vocal and nervous about us potentially interrupting utilities to their operations. There are dozens of biotech companies working on issues like curing cancer and genetic testing. So we’re doing one-on-one briefings, company-wide meetings, and we also have a very specific emergency plan.”
Until the plant is working smoothly, Jones will continue to stay on top of community outreach. She welcomes the challenge. “There were so many times when I thought, ‘Will I have a job?’” she says. “The ups and downs have been frustrating. We’d have high highs, and then a week later a lawsuit would be filed. It’s been a roller coaster ride. But I feel very passionately about the project. It’s not just a job to me. It’s hard to move on from the lows.”
She finds satisfaction in going on-site and seeing the construction underway. “There’s a lot of pressure on Carlsbad,” she says. “Everyone is watching. It’s kind of exciting. It’s our first baby. It’s going to tell a lot when the project is up and running successfully.”
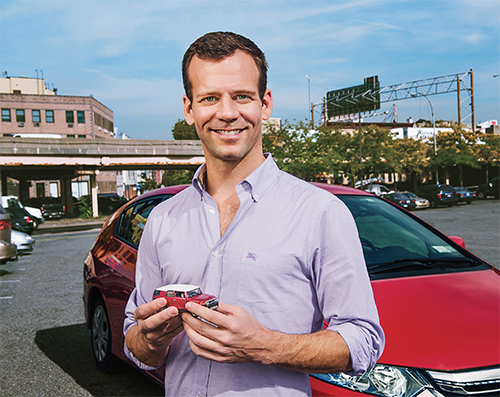
Photo: Laura Barisonzi
Ed O’Malley, MBA’03: It’s hard to overstate the importance of energy sources in the world today.
Exploring New Horizons
When an idea comes to Ed O’Malley, MBA’03, he doesn’t let go of it easily. Around third grade, he went to space camp. Returning home with dreams of space exploration filling his head, he decided to become an engineer and, eventually, an astronaut. As the years went by, O’Malley didn’t waver. He studied mechanical engineering at Johns Hopkins, and then took a job as an aerospace engineer doing probabilistic risk assessment of the space station. “I was 22 and still wanted to be an astronaut,” he says.
O’Malley enjoyed the job, working on different systems of the space station and traveling to the Johnson Space Center in Houston to perform various analytics. Slowly, however, something else did begin to capture his attention. Startups. “It was the end of the Internet boom. Companies were failing. But I was still intrigued by the idea of creating a company and product from scratch,” he says.
After more than 15 years of working toward one dream, O’Malley found himself at a crossroads of sorts. He decided to let go of his space aspirations and turned his attention to new ventures. “Problem was,” he says, “I didn’t know the first thing about business.” In fact, he had avoided the subject entirely because his mother had pushed the idea of pursuing a business career on him; like many youth, he reacted by doing the complete opposite. “I should have paid more attention to her,” he says. To fill the gap, O’Malley came to Babson, choosing it because of the College’s reputation in entrepreneurship.
Following his degree, O’Malley explored a new launch (but didn’t bite), helped found a company that manufactured diesel auxiliary power units (it has since closed), and was looking for his next move when he learned from a former associate about the availability of a patent for a novel new car engine. According to O’Malley, the design of the engine, developed by machinery manufacturer Caterpillar, was a major departure from conventional architectures, being one-quarter the size of typical engines and significantly more efficient. Benefits could include cheaper production costs, lower emissions, and reduced fuel consumption. The concept had been tested in computer simulations, which indicated the idea could work, but investing in a new technology didn’t interest Caterpillar. So the manufacturer gave Kansas State University the patent in exchange for a large tax break, and the university was looking to commercialize the product.
“My first reaction was if this engine is so amazing, why aren’t others clamoring to do something with it?” says O’Malley. Still intrigued, he met with people from Kansas State and, more importantly, the inventor, John Clarke. Clarke explained the concept in detail, and O’Malley started to get it. He also felt a connection to Clarke. “He’s a truly world-class guy and believed in the promise of the engine,” says O’Malley. Soon, O’Malley did, too.
Although the engine was just in the early development phase, and the associated risk was huge, O’Malley went for it. He convinced Clarke to join him, negotiated and obtained the rights to the patent, and founded Motiv Engines. That was almost five years ago. Since then, O’Malley and Clarke completed the design and began testing. They built a prototype to figure out what does and doesn’t work and have gone through at least four cycles of altering the design, simulating and fabricating revised parts, and then building and retesting the updated engine.
“By far the most exciting milestone was the first time the engine fired,” says O’Malley, which was in late 2011. “The first time we got it ready, put fuel in it, and heard that tone change from pumping air to firing, and then smoke came out of the tailpipe. That was exciting.”
The fundamental theory worked the way they predicted it would. But the two ran into “mundane problems,” as O’Malley calls them. Because the design used parts in different ways than they were intended, parts would leak or otherwise fail. More redesign and testing followed. “We were working on another redesign to solve problems,” he says, “and John had an epiphany. He came up with a completely new approach to the thermodynamics that is simpler and uses available technology in conventional ways, so it should be more durable.”
The new design, says O’Malley, will be a complete overhaul but offer the same potential improvements over conventional engines as the previous design. To help bring it to fruition, he has hired two more engineers and leased office space for everyone to work together in New York City. A year from now, O’Malley hopes to have the engine running and producing data. “My timeline gets fuzzier after that,” he says, but getting to market could take another four years. Of course, O’Malley then would have to convince car manufacturers that his engine was worth considering. “One of our tasks is to make that switch as easy as possible,” he says.
Going back to the drawing board after five years of seeming progress would cause many people to give up, but not O’Malley. He’s invigorated and excited by the prospect of the new design and confident his team can make it work. The end vision is what really keeps him motivated. “It’s hard to overstate the importance of energy sources in the world today. This engine is more efficient, so it consumes less fuel. When you have constrained resources, that’s important. It reduces emissions, which have a negative impact on the environment. It can lower the cost of car production, because it’s smaller,” he says. “It’s the first real major step-change in engine efficiency in the past 100 years.”